Refining
WHAT WE DO
The heart of the Group is the Sarroch refinery, the largest in the Mediterranean in terms of production capacity – over 15 million tonnes per year, equal to 300,000 barrels per day –
which contributes approximately 20 percent to Italy’s refining capacity – and it is one of the most advanced in terms of plant complexity (Nelson Index of 11.7).

The industrial site, operated by Sarlux, is located on the south-western coast of Sardinia, in a strategic position in the Mediterranean Sea, ensuring proximity to several oil-producing countries and to the main markets for refined products.
The refinery is equipped with advanced technology plants performing both separation (e.g. distillation) and conversion processes (catalytic and thermal) and able to adapt the steps of the production cycle to the characteristics of the crude oil to be processed, so as to obtain high-grade and more environmentally-friendly oil products.
PRODUCTION PROCESSES
In terms of technology, a key strength of Sarlux production is the integration of the oil refining cycle with electricity generation: this allows the facility to maximise the conversion of raw materials into valuable products and energy.
Our refinery sets a benchmark in the industry for efficiency and environmental sustainability, thanks to the know-how and technological and human resources we have built in over 50 years of activity.
The integrated production process, described in the section of the website Interactive tour of the refinery, is developed through a series of process units which, over the years, have undergone several technology upgrades to make them more efficient and environmentally friendly.
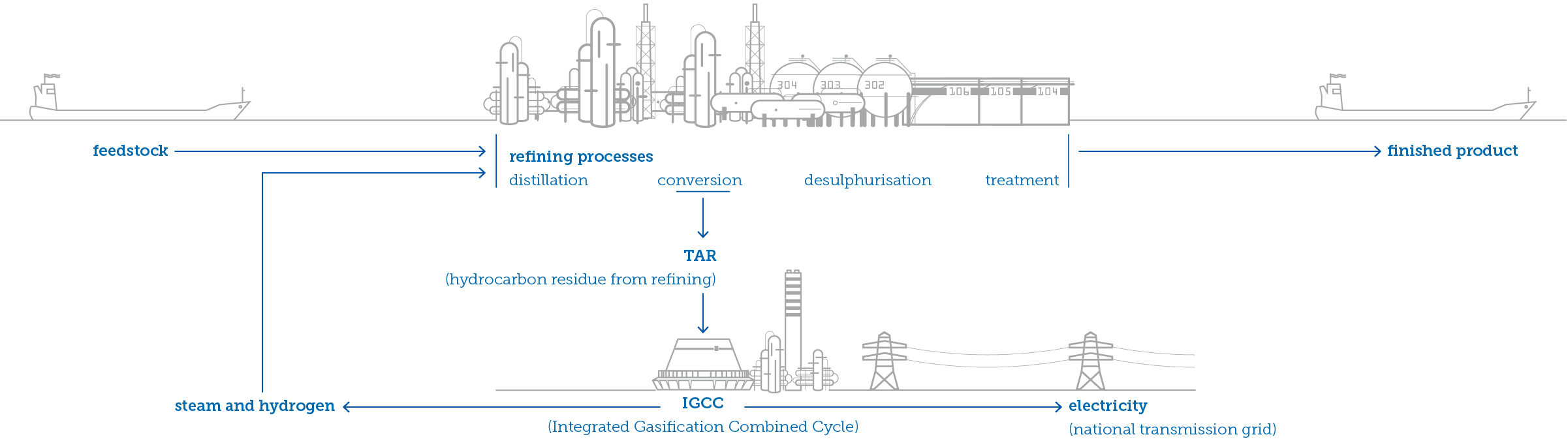
Steps of the refining process
Topping (atmospheric distillation) and Vacuum (vacuum distillation) are the crude oil distillation units for the production of the primary fractions:
- heavy gas oil
- kerosene
- naphtha
- butane
- propane
Mild Hydro Cracking (MHC), Fluid Catalytic Cracking (FCC) and Visbreaker are the conversion units where hydrocarbons and heavy distillates are transformed into medium-light fractions:
- gas oil
- naphtha
- propylene
Catalytic Reforming (CCR) is the unit that converts light distillates (naphtha) into high-octane products. The process also yields hydrogen, which is used in the desulphurisation process.
The PSA unit recovers and purifies hydrogen for use in the desulphurisation unit.
The desulphurisation units treat middle distillates (kerosene and gas oils) with catalytic hydrogenation processes to remove sulphur and improve product quality. In particular, unit U800 of the catalytic cracking plant enables the production of low-sulphur gasoline.
Tert-Amyl-methyl-ether (TAME) improves the quality characteristics (alkylation) and performance of gasoline.
COMPLEXITY AND FLEXIBILITY
Crude oils are not all alike: they may differ significantly in performance, viscosity, yield and density. Each type of oil requires the appropriate refining processes; what makes the difference between refineries is precisely the ability to process a broader range of crude types.
The high flexibility of the Sarlux plants allows them to process a wide range of crude oils from over 30 countries around the world, making the Sarroch site a world leader in the refining industry.
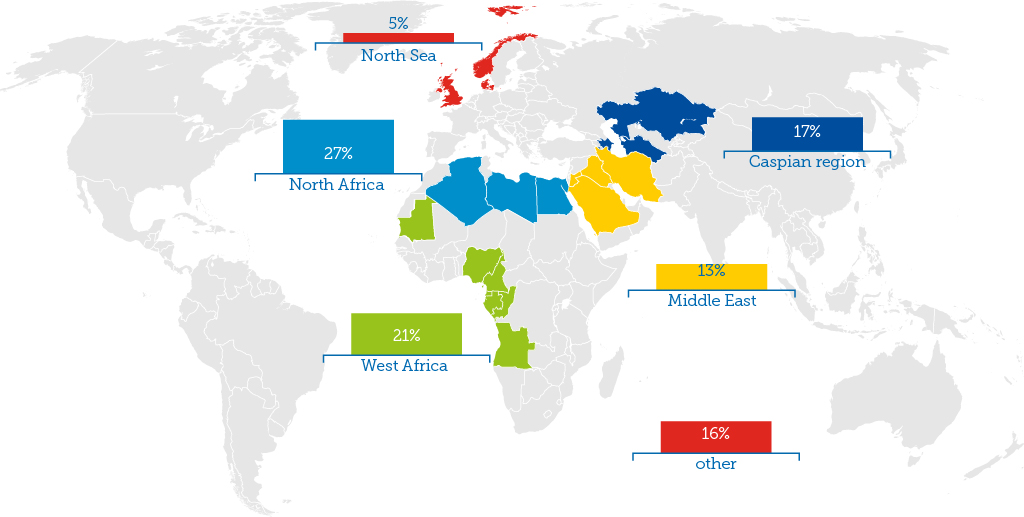
The raw materials (crude oil and fuel oils) delivered to the plant for processing mainly come from the Mediterranean area (North Africa and the Middle East), Caspian Region, Western Africa and North Sea.
The refinery’s capacity to handle a range of feedstocks was achieved also thanks to the commitment and skill of Sarlux’s engineers and operators, who constantly adjust appropriately the process units’ settings to the characteristics of the different crude oils.
Sarlux has focused on this added value, and the refinery’s current performance is the result of an investment strategy resting on three pillars:
- applying the best standards in human resources development
- continuous plant improvements and upgrading
- developing a flexible and trading-oriented industrial facility.
SUSTAINABILITY
The Group is constantly committed to producing high-quality,
environmentally friendly fuels for an increasingly sustainable future.
The refining cycle is fully integrated with the IGCC plant:
The integrated gasification combined cycle plant generates electricity and heat from the heavy hydrocarbons produced by refining, which are normally converted into fuel oil.
Through the IGCC (Integrated Gasification Combined Cycle) plant – installed capacity of 575 megawatts – over 3,5 billion kilowatt hours (kWh) of electricity were generated in 2023. All the electricity produced is sold to the Energy Services Operator (Gestore dei Servizi Energetici – GSE SpA).
RECYCLING
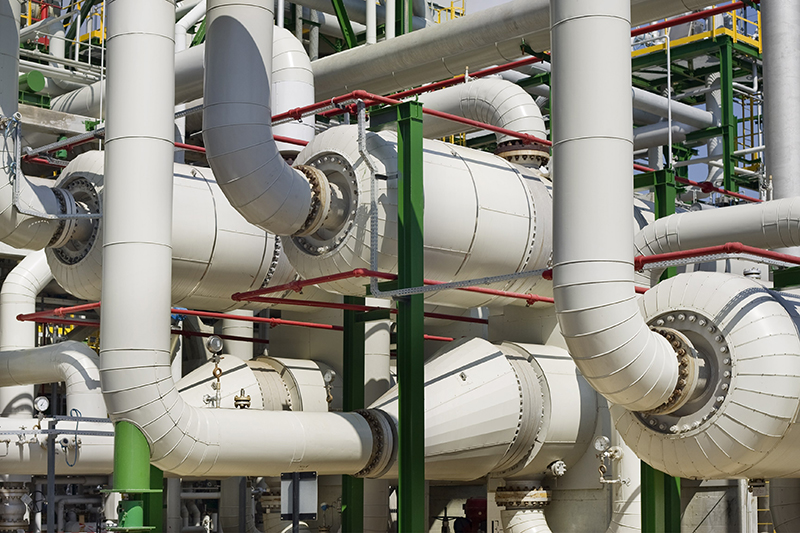
The Visbreaker sends the heavy hydrocarbon residues (TAR) to the IGCC plant for the production of electricity.
The DEA units remove the sulphur compounds (H2S) from the non-condensable fuel gas and enable its reuse in the refining processes.
The Tail Gas Treatment Unit (TGTU) treats tail gases increasing the recovery of sulphur, which is used in chemistry (sulphuric acid for batteries), agriculture (fertilisers and insecticides) and in the pharmaceutical industry. This recovery process reduces air emissions of sulphur dioxide (SO2).
Water treatment plants produce recycled water covering about 30% of the total needs of our facility’s process units.
ENVIRONMENTAL QUALITY
Sulphur content is a key indicator of the environmental quality of refinery products. Low sulphur content means that fuels will produce less emissions and hence will have a lower impact on the atmosphere.
Throughout the entire process, from the choice of feedstock to the fitting of efficient desulphurisation systems, Sarlux has always deployed the best techniques to make its processes more environmentally friendly. Through these investments we have greatly improved our refinery’s desulphurisation capacity.
Sarlux was one of the first refineries in Italy to stop producing leaded gasoline, before it was required by law.
This was achieved largely thanks to our Catalytic Reforming unit (CCR), installed in 1983, which made the use of lead unnecessary. We implemented a number of other measures to improve product quality and environmental compatibility before they became required by law; an example is the use of double-hull tankers.
OUTPUTS
The Sarlux plants in Sarroch supply the whole of Sardinia with fuels and electricity (covering about 42% of the island’s demand in 2023).
As regards oil production, it can be seen that in 2023 the yields of middle distillates reduced in favor of greater production of semi-finished products, fuel oil and naphtha.
The refinery’s products are mainly delivered to the central and western Mediterranean region.
diesel and kerosene
gasoline and naphtha
VLSFO (fuel oil)
LPG
C&P (consumption and losses)
other
Refined products
(source site Saras)
STORAGE
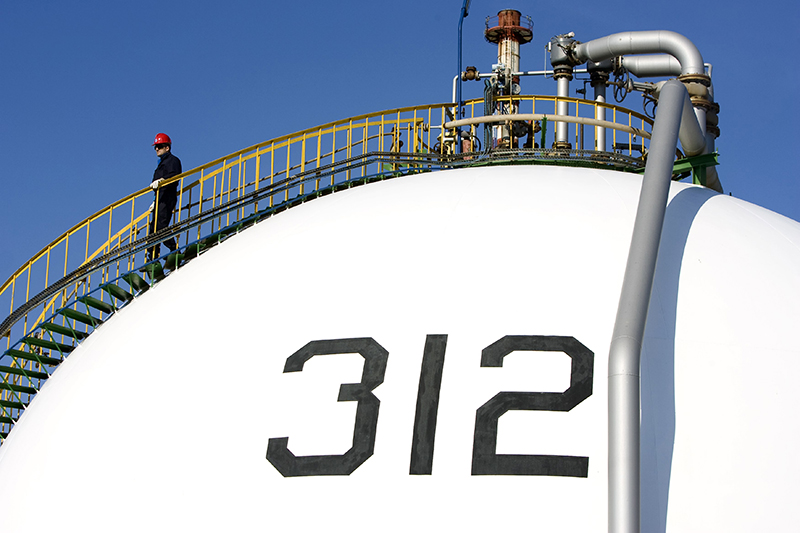
The raw materials and finished products are stored in the Tank Farm, while excise-duty paid products are held in the National Storage Facility, located outside the ‘bonded area’. Liquefied gases (LPG) are stored in pressure tanks, called ‘spheres’, ‘bullets’ and ‘horton spheres’.
The logistics structures consist of 202 tanks for approximately 4 million m3 of storage.
All tanks are fitted with permanent fire-prevention systems and containment basins in reinforced concrete and with concrete floors, or with earth banks,
to isolate the products and protect the soil from leaks.
The fire prevention system in the LPG storage areas is controlled by a device that monitors a set of parameters (including wind direction) to activate fire-prevention and leak containment measures where necessary. To prevent accidents, the LPG tanks are also equipped with pressure monitoring and unexpected pressure surge relief systems.
OTHER STRENGTHS OF THE SARLUX REFINERY

Size
300,000 refined barrels per day
about 20% of Italy’s total capacity
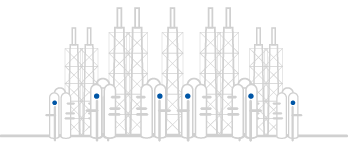
Complexity
light and middle distillates 88,5%
Nelson Index of 11.7
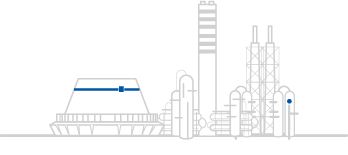
Integration
perfectly integrated IGCC plant
(the heavy residue is converted into electricity, hydrogen and steam)
integrated petrochemical plants
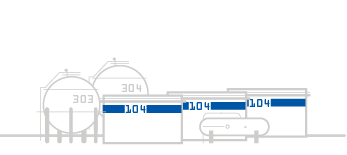
Logistics
13 berths for oil tankers
3,8 million m3 of storage capacity
High flexibility and advanced technology have made Sarlux a great refinery, in terms of both processing capacity and complexity. Our refinery ranks in the top league in Europe – we are perfectly positioned to capture the opportunities offered by the oil market, exploiting a wide range of crude oil grades.
The Saras Group has built a supply chain tying seamlessly our production operation with the commercial side, which is managed by our subsidiary Saras Trading SA, based in Geneva.
